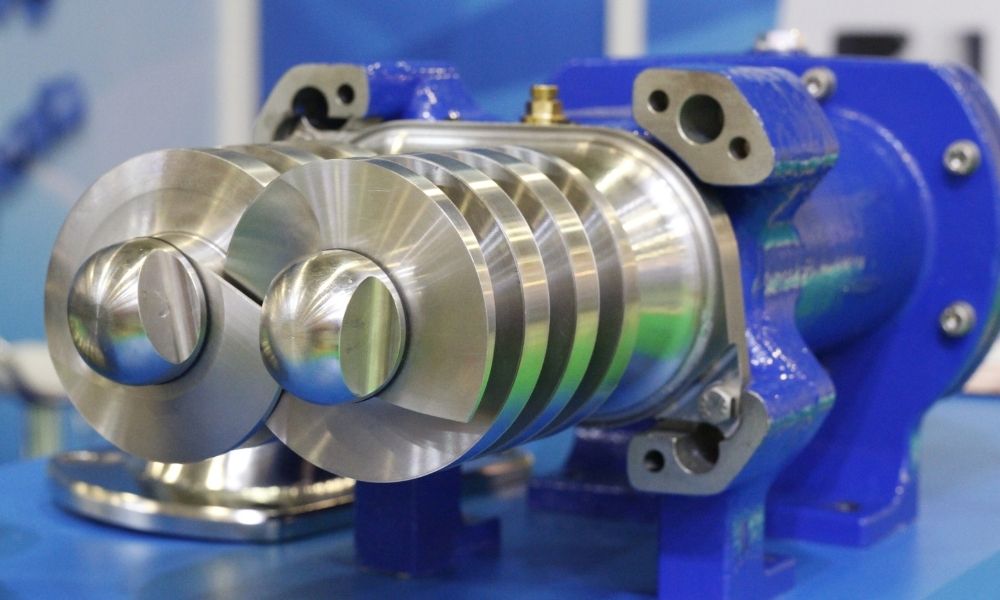
Peristaltic Versus Diaphragm Metering Pumps
July 19, 2021The degradation of pumps is normal; everything deteriorates over time. But you need to know what to look out for. With industrial pumps, the dangers may extend beyond decreasing efficiency. They can contaminate the system with bacteria and inadvertently poison those drinking from or using the system.
No matter the setting, these four reasons of industrial pump failures to know about largely remain the same. Keep in mind any deficiencies in the system and determine what may be wrong. Let’s learn about reasons for industrial pump failures.
1. Cavitation
When liquids run through your pump system, you need to ensure sufficient pressure moves everything along. If the pressure is too low, the liquid may turn to vapor. This can then lead to bubble formation in the pump. These bubbles can implode, causing shockwaves that physically strain the system. Inevitably, this will result in pitting on the inner surface of the pump.
2. Corrosion
Corrosion happens when chemicals react to the metal of the pump and cause oxidation. Different metals handle corrosion differently. Many manufactures opt for stainless steel, as it resists corrosion and is available at a relatively inexpensive price point. Another alternative is cast iron. No matter what material you decide on, corrosion is still a possibility and can decrease the efficiency of your pump.
3. Fouling
Even with liquid flowing through your system, small particles may enter it. When they do, they can cause undue stress on the pumps and force them to work harder. In some of these scenarios, fouling occurs. Fouling is when particulate matter adheres to the inner walls of your pump, decreasing flow capacity and, in bad cases, resulting in blockages.
4. Wear And Tear
Even without corrosion or bubble implosions, your pumps may still experience natural wear from small particulate matter in the system. Small particles with sufficient coarseness can scrape the inside of your pump, scratching its walls and wearing down its lining. This physical damage to the inner walls causes the pump to work harder to transport material, overburdening the system and decreasing efficiency.
Be Aware Of Issues
No matter what reasons for industrial pump failures you may experience, you must always monitor your system and note any changes in quality and efficiency. Small discrepancies may be clues to growing problems that you must solve before they result in severe damage to your equipment.
If you’re facing problems with your pumps, contact Simply Pumps. We’re an industrial pump supplier with over a decade of experience installing, servicing, and improving pump systems.